The Action Tool and Manufacturing Difference
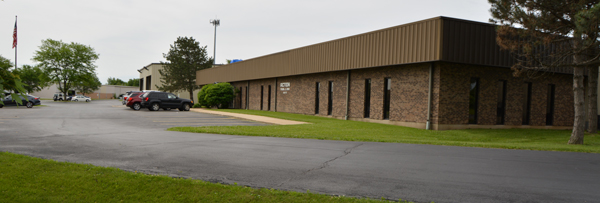
Action Tool and Manufacturings decades of experience in the tooling and stamping industry affords the potential customer numerous benefits. The case studies above exemplify common areas that this experience has saved customers money. The elimination of secondary operations, scrap reduction, accurate repeatability, ability to hold tighter tolerances out of the tool, decreased time to market, all translate to one thing.. A cost savings to the customer!
How can Action Tool save you money and time? Contact us to learn more.
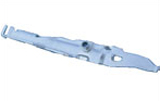
Automotive Customer, Latch
Weld, secondary pierce die, and stamping operation eliminated by conversion to progressive die complete stamped part.
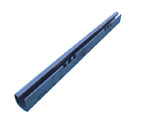
Automotive Customer, Track
Initial roll formed part converted to progressive dies complete. Three secondary operations eliminated. Progressive complete parts able to consistently meet tighter tolerances.
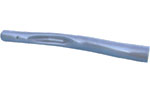
Off Highway Vehicle, Tube
Progressive complete process eliminated secondary operation. Eliminated secondary pierce operation as well.
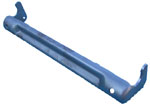
Automotive Customer, Bracket with Ears
Three parts consolidated into one. Reduced part numbers to track and order. Elimination of secondary operations including welding and machining.
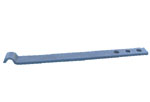
Automation Equipment Manufacture, Strap Clamps
Insert die designed to accommodate the manufacture of three parts; center, left and right. Three operations eliminated. A progressive complete tool and process eliminated cutoff, form, and pierce operations.
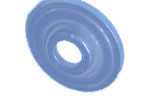
IT Customer, Track Roller
Traditional bar stock machined component converted to metal stamping. Conversion to stamping from screw machined part greatly reduced piece part price with out compromising part performance.
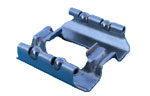
Automotive Customer, Ball Retainer
Bearings installed in the press eliminated secondary operation.
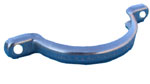
Automotive Customer, Turbo Bracket
Blank, Form and Pierce operations eliminated in part conversion to progressive die complete.
Request a Quote